Overview of Automotive Paint
The automotive/motorcycle paint industry is undergoing a strong transition to environmentally friendly paints, with water-based paints gradually replacing solvent-based paints. Advanced additives for automotive paints are increasingly favored, meeting the demand for environmentally friendly paints in Vietnam. Advanced raw materials help reduce VOC levels, support the development of water-based paints, high solid content paints, and solvent-free paints. These additives not only replace traditional solvent-based paints but also optimize the paint formula and application process to improve performance, protect the environment, and reduce costs.
Additives for Automotive Paint
Evonik Chemical Group is a leading manufacturer of environmentally friendly raw materials for all types and systems of automotive/motorcycle coatings. Evonik’s silica-based additives help adjust the rheological properties in automotive paint, allowing manufacturers to address issues such as wetting, defoaming, flow, etc., as well as achieve the desired surface effects.
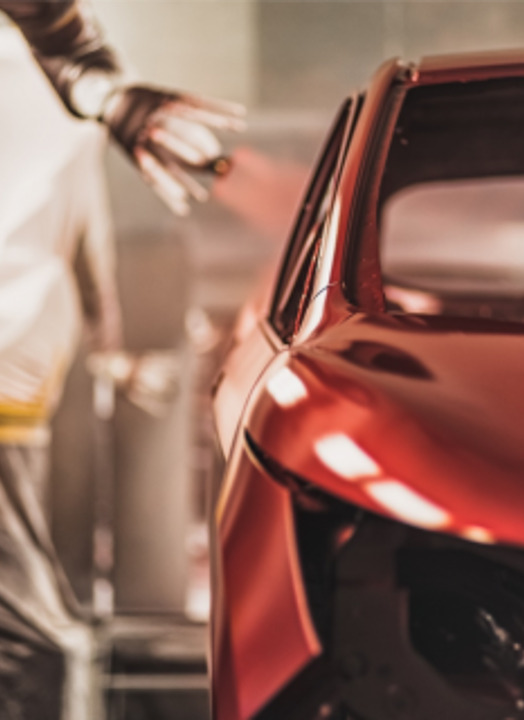
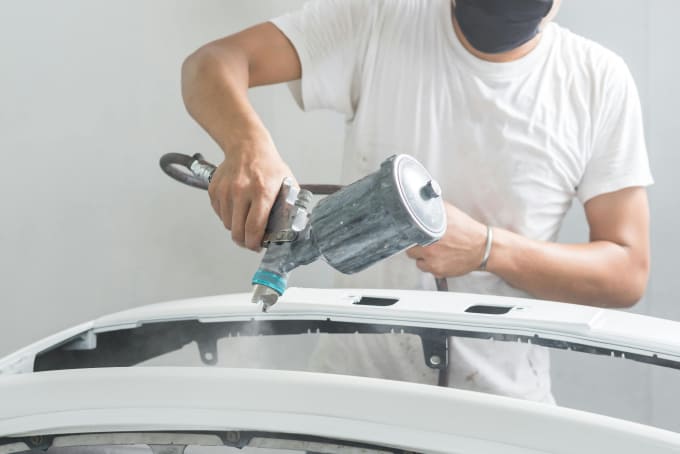
Automotive primer conductive additive
The application of Graphene Nanotubes (TUBALL™ MATRIX) provides a solution to reduce the surface resistance of automotive primer, while maintaining color and optimizing costs. Compared to conductive carbon black, TUBALL™ MATRIX offers superior benefits:
- Clean production process, no carbon dust generated
- Low dosage, increasing flexibility in the final formulation
- Easy to apply, simplifying logistics and improving efficiency
- Compatible with various paint systems (water-based or solvent-based) and multiple resin types (acrylic, epoxy, etc.)
High performance materials for the automotive industry
The automotive, transportation, and aerospace industries are constantly seeking optimal material solutions to meet the demands for enhanced operational performance and safety of vehicles. Polyamide 11 (Nylon 11) and Polyamide 12 (Nylon 12) are known as one of the high-performance material solutions due to their lightweight, chemical resistance, excellent heat resistance, high mechanical strength, and design flexibility. Furthermore, Polyamide 11, derived from 100% plant sources, helps reduce the environmental impact of the automotive and transportation industries. This not only helps car manufacturers comply with environmental regulations but also creates sustainable value for customers and the community.
Electric vehicle material solutions
Rilsan® Polyamide 11 (orange color) is designed for crosshead extrusion and injection molding to insulate busbars in electric vehicles.
Rilsan® Polyamide 11 is a fine electrostatic powder coating for metal, providing an excellent material solution for busbar insulation.
Kepstan® PEKK is used for busbars or other components in electric vehicles that require extreme heat resistance, especially in cases of heat dissipation, ensuring reliability at high temperatures.
Material solutions for vehicles using internal combustion engines
Long-chain polyamide materials Rilsan® Polyamide 11 and Rilsamid® Polyamide 12 are excellent materials for components and parts in internal combustion engine vehicles due to their combination of outstanding flexibility, excellent mechanical strength, thermal stability, and significant chemical resistance.
- Fuel lines
- Cooling system vent tubes
- Emission control systems
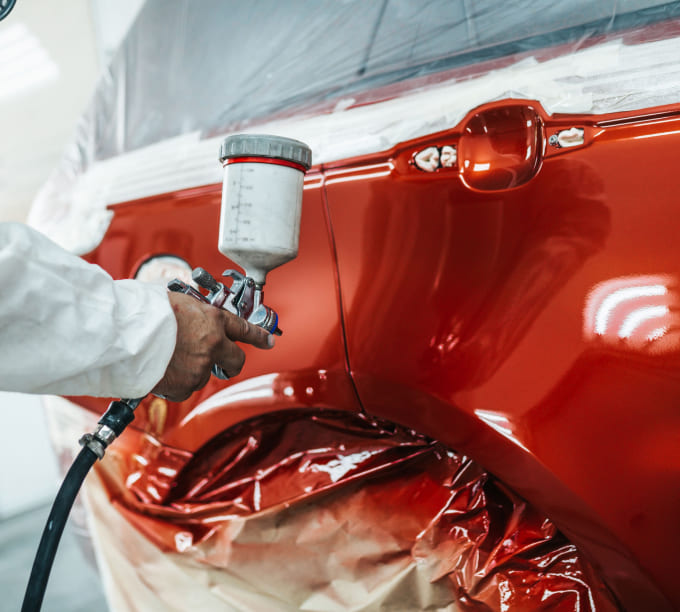